Ginori 1735 in the name of sustainability, designing the Manifattura of the future
Unique savoir-faire, the result of centuries of artistry, becomes high-tech in the name of sustainability. This, in a nutshell, is the unifying thread of the “New Production Kilns” project, recently concluded by Ginori 1735, the expression of the Italian excellence in the field of luxury and lifestyle, one of the world’s leading brands in pure porcelain and in the design, at the Sesto Fiorentino Manifattura, with the installation and successful start-up of 5 environmentally sustainable static porcelain furnaces for firing and production, replacing the 2 outdated and inefficient continuous-cycle kilns previously in operation.
The new kilns, with intermittent firing, guarantee substantial reductions in the environmental impacts from production, with a 62 percent cut in energy consumption and 57 percent cut in CO2 emissions compared to the previous kilns, thanks to a project designed well before the energy price hikes and inflationary pressures of recent months.
But that’s not all. Ginori 1735, in fact, has taken this opportunity to come out ahead in the area of a major new challenge: the design of the Manifattura of the future. A place that can bring about a merging of the artistic talents of the people and the most innovative technologies, where the efficiencies derived from automation guarantee the absolute excellence in every detail that has always summed up the magnificent obsession of Ginori 1735.
The replacement of the kilns has given Ginori 1735 the opportunity to rethink the entire factory around its key resources, at the centre of the new project, allowing a complete renewal of the production layout, with an optimisation of product and information flows through the creation of one large internal team. In addition, thanks to digital technology, different departments are now able to analyse production information through remote monitoring, and work and learn together. Further, the new kilns enable important improvements in the ways of working of the human resources of the Manifattura, allowing the elimination of the night shift, the distancing from heat sources, and a work mode in an air-conditioned environment.
Thanks to the new layout, it is no longer the kiln that “dictates the rules” of production: instead, the great team of passionate, dedicated and extremely specialised master artisans of Ginori 1735, with the automation of selected activities, can finally and totally unleash their creative talents, in a new open space where the different teams collaborate and operate customised machinery based on their savoir-faire. This is a layout, in short, where technology supports the tradition and the absolute artistic beauty of the Manifattura.
“This is a full-circle transformation in the sign of sustainability, connecting the restyling of the factory with the restyling of the offices. Thanks to this project, Ginori 1735, on the strength of its centuries-old history, is ready to face next years of activity in the best possible way, effectively and efficiently preserving the great artistic tradition of the brand. The project, in a nutshell, allows us to project the legacy, savoir-faire and skills of our masters into a high-tech future, where technology supports the artisanal tradition,” commented Alain Prost, Chairman and CEO of Ginori 1735.
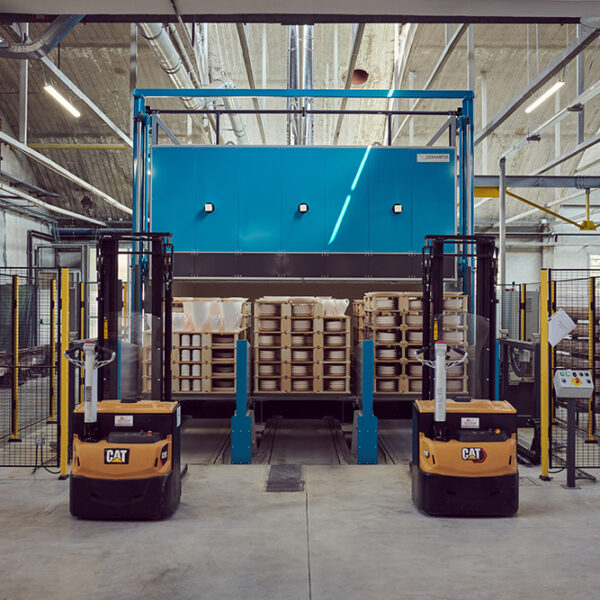